
Katatheon
Farms
Case Study: Using legacy PLC equipment and software to save multi-million dollars worth of greenhouse crops
Overview
Katatheon Farms are a large scale greenhouse operations that grows peppers and tomatoes in Langley, British Columbia. They use large natural gas boilers to keep the crops warm during the cold winter nights.
​
A pipeline explosion in Northern British Columbia forced Fortis BC to give their commercial clients a 24 hour notice that their natural gas supply was going to be shutoff.
Katatheon Farms was affected by this and needed emergency service on their wood burning boiler to save millions of dollars worth of crop.
​
Alliance Power was contracted to get their backup boiler up and running within 24 hours.
​
Our Solution
Our goal was to clear a PLC fault that was preventing Katatheon's backup wood boiler from operating in a timely manner with a limited time frame.
​
The 24/7 service that we provide our clients ensured that we would have a resolution accomplished regardless of the time of day.
​
The wood boiler's legacy PLC hardware and software was no hurdle for us. Using our arsenal of legacy software and programming cables we were able to communicate to this older PLC and get the backup boiler running in time to save the plants from freezing.
Their Challenges
1
Backup Wood Boiler Non-Operational
​
-
Only backup boiler was offline and non-operational due to a PLC fault
​
-
Unable to troubleshoot and resolve issues on their own​
2
24 Hour Timeframe for Resolution
​
-
Limited time to get the backup boiler working
​
-
They needed to find a reputable and reliable firm to provide immediate service -- one that will guarantee a successful resolution​
3
High Loss Potential
​
-
Millions of dollars worth of crops could be destroyed if there is no heat pumped into the greenhouse
​
-
Removing dead crops and re-planting would be expensive, costly and will require extensive reesources
4
Legacy PLC Hardware and Software
​​
-
Outdated Legacy equipment results in hard-to-find support without requiring any new hardware or software purchases
​
-
Unable to clear PLC Fault on their own
​
-
Limited timeframe requires quick turnaround time, high attention to detail, and a skilled error-free fix
​
Identify source and cause of PLC fault using legacy software and programming cables
Clear PLC fault, troubleshoot and commission system to ensure there are no further hidden errors
Installed backup power system and replacement battery for the PLC to prevent issues from arising again
Provided options to migrate legacy PLC to a modern PLC with minimal downtime and minimal cost
Client Achievements
$MM of crop saved
PLC Backup System up and running
Wood boiler operational & peace of mind achieved
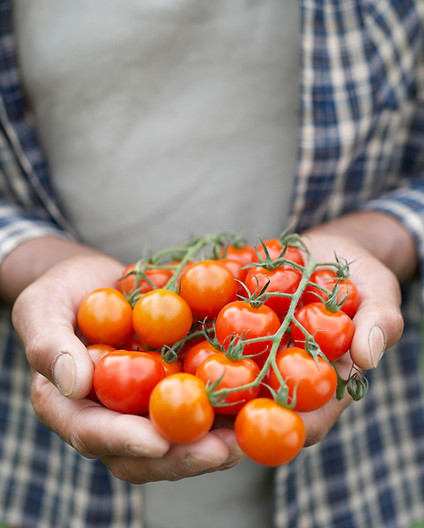